Manufacturing high-quality cable assemblies since 1991
Cablepoint: Making Interconnect Simple
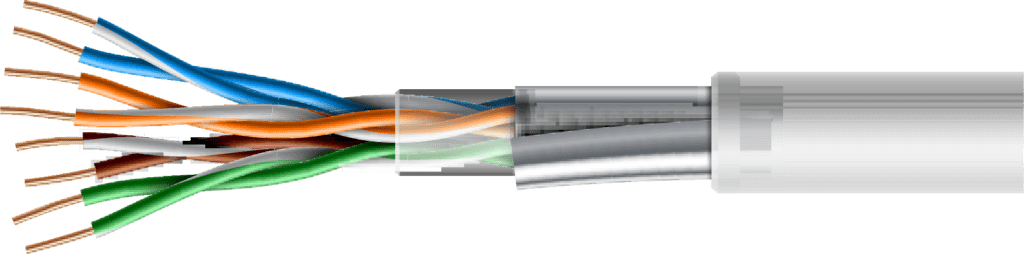
Cablepoint engineer your existing cabling product to enhance quality, offer cost-down initiatives and improve efficiency.
Established in 1991, Cablepoint has been manufacturing high-quality cable assemblies for over 30 years.
We work within a wide variety of industries including pharmaceutical, military, electric vehicle, agricultural, traffic management, beauty and domestic heating appliances – from global enterprises to small businesses.
We work to IPC620 standards and ensure that they’re consistently met through our strict quality processes.
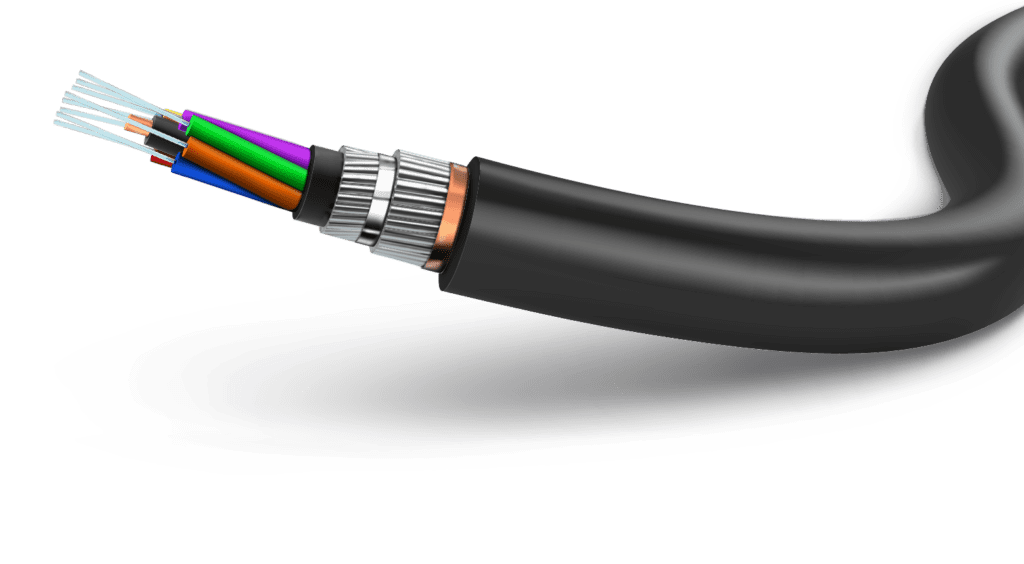
Production Capabilities
From simple wiring looms to complex harnesses, we can produce any required quantity. We also offer a refurbishment option on products, if required.
We produce a wide range of box build and control panels for a number of industries - from pharmaceutical to boiler manufacturers.
We have custom overmould and potting facilities on site. Depending on the cables required, the cost of any tooling can be amortised across your contract.
Our team is IPC trained, with experience producing a wide range of cable assemblies. From simple stripped, tinned, bootlaced and crimped wires to soldered wires and PCB connection.
We provide initial, pre-production cables to ensure complete accuracy, followed by full batch production. Customers may also use this facility for engineering prototypes and design ‘first-offs’.
We have two automated terminating machines with a tinning facility, enabling quality crimped wires to be produced economically and efficiently in large volumes.
Our clean room facility facilitates the production of high end F.O.D (Foreign Object Debris) sensitive specialist cables.
Our Manufacturing Process
From initial contact and assessment, you’re in safe hands.
From your drawing or sample cable, we will source parts and provide you with a quotation, as well as suggestions for improvements and cost savings.
A prototype will then be produced for your approval, accompanied by a Initial Sample Inspection Report (ISIR), before we then manufacture the full order.
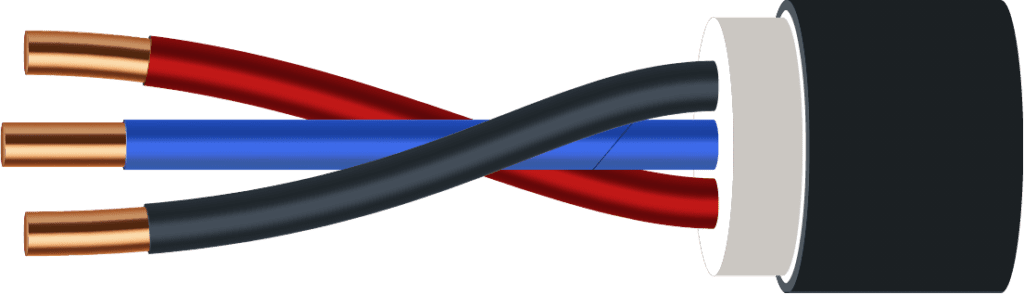
Equipment and Facilities
The Artos and JST termination machines with crimp force monitoring have the ability to crimp extremely small terminations in large volumes, as well as larger crimps, efficiently and accurately.
Providing efficient and accurate work, the clamping force is automatically adjusted to the stripping force, preventing indentations on any sensitive installations. The screen also allows accurate strip lengths and gauge depths to be set.
Used to test the force required on all crimping according to UL & SAE AS 57928 requirements, stranding & AWG.
We have a number of bench strip and crimp machines, which are used to facilitate accurate cutting, crimping and stripping.
Our moulding machine and potting facilities allow us to service the moulding of connectors via injection moulding and overmoulding, as well as producing custom jigs.
Allowing us to apply a range of 0.14 to 2.5mm bootlace ferrules efficiently and accurately.
Our test equipment is used to map each connection of an individual cable and provide test data reports, allowing us to identify any discrepancies.